info@roller-shutter.uk 01392270218
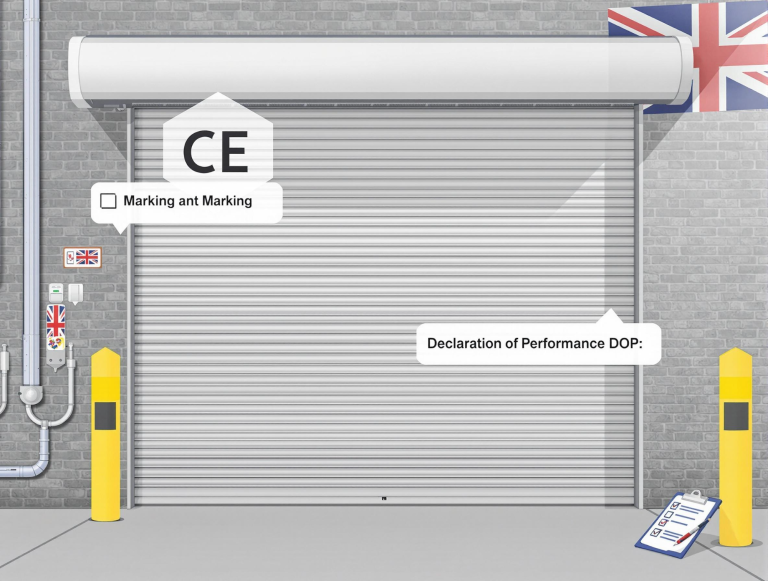
Understanding Regulations: Navigating Roller Shutter Regulations in the UK - A Guide for Businesses
For any business operating in the UK, ensuring your roller shutters and security shutters comply with current legislation is not just a legal requirement but a critical aspect of safeguarding your property and personnel. This comprehensive guide delves into the essential UK roller shutter regulations, focusing on vital areas such as safety standards, CE markings, and specific fire regulations. Crucially, we'll also highlight why choosing a compliant roller shutter installer who adheres strictly to these standards is paramount, as not all companies operate with the necessary rigour, potentially exposing your business to significant risks.
Why Regulations Matter: Safety, Compliance & Responsibility
Roller shutters are classified as machinery and, particularly in commercial and industrial settings, they fall under stringent health and safety legislation. Adhering to these regulations is essential to:
- Ensure Safety: Prevent accidents, injuries, and fatalities caused by malfunctioning or improperly installed shutters.
- Legal Compliance: Avoid hefty fines, legal prosecution, and potential imprisonment for non-compliance.
- Protect Your Business: Prevent operational downtime, invalidate insurance policies, and maintain your reputation.
- Demonstrate Due Diligence: Show that you, as the responsible person, have taken all reasonable steps to provide a safe environment.
Ignorance of the law is no excuse. The responsibility for ensuring roller shutter compliance rests firmly with the business owner, employer, or facilities manager.
Key UK Regulations & Standards for Roller Shutters
Several key pieces of legislation and standards govern the manufacture, supply, installation, and maintenance of roller shutters in the UK:
- The Supply of Machinery (Safety) Regulations 2008 (implementing the EU Machinery Directive):
- This is fundamental. It requires that new electrically operated roller shutters are designed, manufactured, and installed to be safe. Manufacturers must conduct a risk assessment and ensure all relevant safety mechanisms are in place.
- BS EN 13241-1:2003+A2:2016 – Industrial, Commercial and Garage Doors and Gates. Performance requirements and safety:
- This is the primary product standard for power-operated doors and gates, including most roller shutters. It sets out performance characteristics and safety requirements, such as:
- Safety Edges & Photoelectric Sensors: To prevent the shutter from closing on an obstruction, stopping or reversing automatically.
- Safety Brakes/Anti-Fall Back Devices: To prevent the shutter curtain from falling uncontrollably in the event of a motor or component failure.
- Manual Override Systems: Essential for allowing the shutter to be operated during a power failure.
- Emergency Stop Functions: For immediate cessation of movement.
- This is the primary product standard for power-operated doors and gates, including most roller shutters. It sets out performance characteristics and safety requirements, such as:
- CE Marking & Declaration of Performance (DoP):
- The CE marking (and soon UKCA marking post-Brexit) is mandatory for roller shutters covered by BS EN 13241-1. It is the manufacturer's declaration that the product complies with all applicable essential requirements.
- A Declaration of Performance (DoP) must accompany the CE marked product, detailing its specific performance characteristics (e.g., wind resistance class, thermal insulation, safety features). If a product isn't CE marked or lacks a DoP, it is illegal to manufacture, sell, or install in the UK.
- The Workplace (Health, Safety and Welfare) Regulations 1992 (Regulation 5 & 18):
- Places a legal duty on employers and those in charge of workplaces to ensure all equipment, including roller shutters, is safe for use and subject to a "suitable schedule of maintenance."
- The Provision and Use of Work Equipment Regulations 1998 (PUWER):
- Powered roller shutters are classified as work equipment under PUWER. Employers must ensure work equipment is maintained in "efficient working order and in good repair," with safety systems regularly tested. A maintenance log must be kept up-to-date.
- The Electricity at Work Regulations 1989:
- These cover the electrical safety aspects of power-operated roller shutters, including motors and control systems.
Fire Regulations: A Critical Component
For fire-rated roller shutters, specific and stringent regulations apply due to their life-saving function:
- Regulatory Reform (Fire Safety) Order 2005: Places the responsibility on the "responsible person" (owner, employer, etc.) to conduct fire risk assessments and implement appropriate fire safety measures, including the correct installation and maintenance of fire doors and fire shutters.
- BS EN 16034:2014: This is the specific product standard for fire resisting and/or smoke control shutters. It dictates the testing and performance requirements for a fire shutter to be certified for integrity (E), and sometimes insulation (I) and radiation (W) over a specific time (e.g., E30, EI60).
- Automatic Closure: Fire shutters must be designed with a gravity fail-safe mechanism to ensure they automatically close upon activation of a fire alarm or loss of power, compartmentalizing the building to prevent fire and smoke spread.
The Critical Importance of Choosing a Compliant Installer
This is arguably the most vital takeaway for any business. Not all companies fit shutters correctly or to the required standards. Even if you purchase a fully compliant, CE-marked shutter, an improper installation can compromise its safety and performance, rendering it non-compliant and potentially dangerous.
Why your business MUST choose a compliant company:
- Safety Assurance: A compliant installer understands and adheres to the complex UK safety standards and ensures all safety features are correctly configured and tested.
- Legal Protection: If an accident occurs due to poor installation, your business could face severe legal consequences, fines, or invalidated insurance if you cannot demonstrate that you engaged a competent person or compliant company.
- Guaranteed Performance: Only a skilled and compliant installer can ensure the shutter performs as intended by its certification (e.g., meeting its wind resistance class or fire rating).
- Documentation & Traceability: Compliant companies provide full documentation, including installation certificates, maintenance logs, and records of testing, which are crucial for auditing and legal purposes.
- Longevity & Reliability: Proper installation prevents premature wear and tear, leading to fewer breakdowns and extending the lifespan of your investment.
When commissioning roller shutter installation for your business, always ask for evidence of their compliance, accreditation (e.g., industry body memberships, relevant certifications), and track record of working to the highest UK regulations.
Navigating roller shutter regulations can seem complex, but understanding these key standards and, more importantly, choosing a compliant company working to the right regulations, is fundamental to ensuring the safety, security, and legal standing of your business. Prioritise certified products and professional installation for complete peace of mind.